吉阳智云阳如坤:靠规模来解决动力电池制造过程的问题
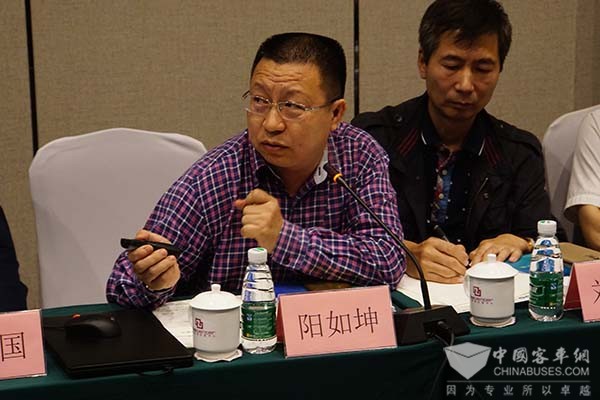
会上,中深圳吉阳智云科技有限公司董事长阳如坤做了精彩发言,内容整理如下:
我们认为(动力电池应)成为一个产业发展的母产品,就是跟CPU、机器人或者钢铁同等重要的一个产品。我们认为这样一种产品应该尽量做到单一化、标准化、系列化,做到做精、做细这样一个要求,也是成为整个产业发展重要的一些方面。这里我想说一下动力电池制造的现状,我下面会有详细的。这里有一个事实我想跟大家说一说,我们看到的规范的目录,我认真的统计了一下,大概有10家,有30多个型号,总部这4批公布的目录下来,大概有56家,一共有150多个型号,刚才比亚迪说他们有4个型号,实际上对于我们国家来说,整个这些型号实际上对我们整个制造产业是非常不利的,这里说是差异化竞争,我认为主要还是技术不成熟,或者很多人自以为是,结果结构不同、工艺不同、装备不同,很难实现技术的积累,制造合格率非常低,整个相当于设备的运转率也低,效率低,成本就居高不下,我认为这点主要还是从型号的角度来解决。
刚才王博士也说到了,规格,我建议你们的规格按照尺寸作为主参数,而不是把容量作为主参数,这样真正才能体现电池的规格。另外我建议,就以这三类,一个圆柱、一个方型的,另外是软包,我个人认为就是6—10种,整个国内我们推荐的标准,不要做太多,太多以后像比亚迪刚才说的,很难把质量提上去,很难把效率提上去。这里还有很重要的因素,从装备制造的角度来看,我们整个制造标准没有,就是说在这块上,我不知道这个应该归到哪一块,是归到整个电池,还是归到装备,还是归到哪里,这个方面的研究是很缺乏的。我举几个例子,比如材料的替代,电池制造过程的一些东西,还有制造的认可、应用的认可。
我个人认为,电池的安全性主要三个方面,设计、制造、使用。设计方面,我觉得基于可制造的电池的设计非常缺乏,我也看国内的一些大企业,我们一些电池的设计,制造方面,制造性考虑相对来说是比较缺乏的,怎么样保证我设计的电池制造的合格率是最高的,这方面值得重视。从制造本身来说,我们主要是从制造的精度、控制、智能制造方面考虑,还有使用方面,当然也是有一些重要的内容。
从制造整个电池来说,在我们看来四个方面,水分、毛刺、极片保护、粉尘的控制,从制造角度来说最重要的保证这几个方面。
这里我想举个例子,这是大家看到的动力电池的内部结构,实际上电池有一个很重要的原则,这里面一旦出现缝隙的时候实际上对电池的性能影响非常大,不管是枝晶也好、沉积也好都在这里产生。我们做了一个实验,我们现在的方形电池卷绕、压扁以后形成的缝隙,我猜大部分的动力电池都会出现这样的问题。这是拆开隔膜的情况,这是隔膜的变化情况。我们认为电池的制造,应该说从宏观的制造到微观,用极光,用这样一些,包括张力控制这些来解决细微的问题,这是我说的这个方面的内容。
动力电池应该说未来从现在的这个现状、合格率低、一致性差,发展成未来大规模的制造,未来能够实现从1G瓦时到5—10G瓦时。实际上1G瓦时什么概念才2万辆车到3万辆车,我们认为从动力电池制造角度来说,我们电池一条线的产能远远太低了,要怎么实现大规模制造是很重要的方面,我们认为动力电池制造主要往两个方面,一个是大规模和智能化这个方面。这里我是给大家算个简单的算术,从合格率到电池的利润率,实际上我们在这里目前电池的现状我们还是非常低,比如我们的合格率只有90左右,我们的材料利用率大概也就是在88,整个有12的利润增长空间,我们认为在未来如果说我们能做到99,利用率做到98的话,我们这里大概增长的空间会更大,我认为制造的角度来说降成本也是很重要的方面。
这是整个电池未来的情况,我就不多说,从体系来说大家都比较清楚,我们认为在未来主要是在制造成本和制造合格率上太体现,我们认为动力电池制造未来就是大规模和智能化这两个方面来入手,来把整个动力电池的制造问题解决,这次我们也是跟肖主任制定了一个制造的路线图,最重要的我认为这里在电池的一致性和品种、和制造的成本上有一些很重要的要做的事情,我们认为在制造成本上,比如说我们现在是制造成本在2毛5,未来我们希望降大几分钱或者1毛钱的瓦时制造成本,分解到制造领域我们怎么努力来达到这样一个目标,这是动力电池制造的路线图。
根据我最近了解电池的安全性,我个人认为我们现在应该启动新型电池的制造研究,这里我了解的,比如说在固态或者半固态锂硫电池的制造工艺上的研究,我个人认为应该现在来启动,比如像我们锂铂的制造,或者核心物质和固态电解质的复合,或者我们隔膜和极片的复合,因为在我看来,确确实实这种固态电池在安全性和能量密度上都带来很有价值的东西,当然可能从产业界的角度来说,我们大规模生产还早,但是我认为在这个层面上是一个机会,或者对我们国内来说是一个机会。
动力电池制造的挑战我认为有以下几个方面,刚才说的尺寸规格,第二,单线的产能能不能提到更高,另外数字化的设计,还有我们制造过程的全监控,还有连续一体化的过程。在数字化设计,有一些电池厂,我认为数字化设计还有很多问题,从本身材料组配型、可制造的设计等等方面还缺乏,还有基于可回收的电池设计,我们曾经探讨532模型,我们先把50%的价值用在这个动力,30%用在储能,20%拿来回收,我认为如果能实现这样一个数字化设计模型,可能对于未来动力电池发展会比较有好处。
从动力电池制造挑战来说,我认为要全生命周期的过程,这里我最强调的一点就是,我们整个电池制造过程的所有影响质量、安全、一致性的要求,能够实现全部的检测、预判和控制,这里面是很有难度的东西,包括要实现,比如我们粉料要实现在线检测是很困难的,但是我们这里不得不研究这些都是,在我看来这里应该立项专门来处理这样一些事情。
我想从未来制造的角度,我觉得动力电池的制造应该从大规模的角度来说,我们一定要强调连续化,因为我发现我们动力电池制造过程都是断断续续的,走一段停一段,很浪费材料、很浪费时间、更浪费我们整个制造过程的质量,这里我想提三个方面,一个是制料的连续一体化的过程,第二制片连续一体化,第三,烘烤,整个暂停是对我们动力电池制造过程影响提高效率大规模很重要的制约因素,这可能是立一些项目解决这个问题。这是动力电池制造过程的互联互通,为智能制造立下标准的地方。我们最近提出一些方法,我们把所有的设备作为一个CPS节点,叫做信息物理单元,也是美国人提出来的,我们把设计作为一个单元来看成一个互联网的节点,这样所有的设备把它作为一个透明的东西,这是我们构建了一个透明工厂的架构。
我们动力电池要达到我们明确的制造目标,希望从整个入料和最后输出的过程实现全检测的控制,这里可以用二维码来追溯。大概我们通过互联互通互操作,会有2000—3000个参数要实现实时的在线监控,我们希望实现几个闭环,第一个,在电芯。第二个,在PACK。第三个,实现整个大规模的数字化制造和闭环控制。
最后我想提一个简单的建议,装备方面,我认为,第一个,我们对工艺的研究不足。第二个,我们影响质量的因素,我们这里还缺乏一些监控。第三个,我们装备的基础确实国内相对来说比较差。我们很多螺钉、螺帽、垫片都很难满足要求,相当于我们整个基础比较差,在差的条件下怎么能保证电池制造本身的稳定性和合格,我认为也是很重要的方面。第四个,我认为电池装备本身存在不健康的因素,我们怎么来解决这个问题。从某种意义上来说,我认为我们重视不足、支持不足、研究不足。所谓重视不足,比如我们在整个电池的发展过程中的立项,很少去专项支持装备、专项支持这方面的内容。从装备角度来说,我们最后拿到的好多都是靠自己一些资金积累来解决这些问题,最后往往是发展过程中很难去把装备做到更好。
这里我有一个简单的建议,第一个,我们应该做一个动力电池制造的路线图,来立项研究电池的工艺、制造方法和制造装备。第二个,从装备的发展来统一规划,专门来立项。第三个,要建立动力电池制造标准和制造装备的标准。从具体的建议来说,第一个,开展大规模、连续化制造技术和装备技术的研究。第二个,智能制造方面。第三个,为2020年或者2020年以后半固态或者固态锂硫电池的制造工艺和装备进行一些准备。我认为这是解决可能那一代电池更重要的方面,当然我们现在业面临很多问题,我觉得现在主要是靠大规模来解决一些制造过程的问题。
1、凡本网注明“来源:www.chinabuses.com” 的所有作品,版权均属于客车网,未经本网授权,任何单位及个人不得转载、摘编或以其它方式使用上述作品。已经本网授权使用作品的,应在授权范围内使用,并注明“来源:www.chinabuses.com”。违反上述声明者,本网将追究其相关法律责任。
2、凡本网注明 “来源:XXX(非客车网)” 的作品,均转载自其它媒体,转载目的在于传递更多信息,并不代表本网赞同其观点和对其真实性负责。
3、如因作品内容、版权和其它问题需要同本网联系的,请在30日内进行。
※ 有关作品版权事宜请联系:copyright#chinabuses.com
- 微宏集团推出全新锂电池电芯和升级版第四代电池包[03-29]
- 加码车辆“用电安全” 森鹏全芯片数字配电批量交付湛江汽运 [11-05]
- 重磅!精进电动登陆科创板 首日涨幅28.45%[10-27]
- 亿华通入选北京市首批首台(套)重大技术装备企业[10-23]
- 喜报!精进电动荣获2020年度上海市技术发明奖项二等奖[10-22]
- 喜报!亿华通荣获2020年度北京市科学技术进步奖一等奖[09-27]
- “涝疫”结合的39天 迪耀科技确保员工工资全额发放[09-03]
- 节能又防疫 | 配备爱普分布式净化全铝车身的国唐汽车交付盐城公交[09-02]